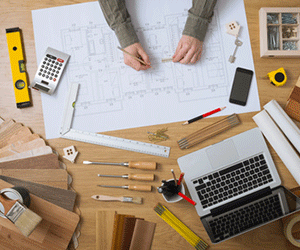
A project manager that fails to allocate project resources is like a carpenter without a hammer.
That’s why estimating task resources is an integral step in project planning. It also happens to be one of the most fundamental aspects of project management, one of the steps that the project manager utilizes on a day to day basis.
Types of Resources
Each task on the task list must be assigned the resources necessary to perform the task.
For small projects there are three major types of resources:
- Labor
- Tools & equipment
- Material & supplies
Labor
Labor is not all created equal. If you try to assign an electrician to install a toilet, you might get some flooding as well as an unhappy employee.
Likewise, if you assign an electrician to design the power plant, you might find your project costs escalating out of control as you try to find more qualified labor during the project.
Thus, in order to correctly define labor you must identify two things:
- Type
- Class
Labor is usually estimated in hours, but can range all the way up to years for megaprojects. In fact, when I was a junior engineer I was involved in a large oil sands project where budgeting and scheduling happened in man-years.
Tools & Equipment
This category generally includes all of the items that do not go into the finished product. Things like drill bits that are used up during a project, or the addition of new tools that the company doesn’t already own. It also includes equipment such as forklifts, vehicles and software.
Often the tools and equipment will be used over multiple projects. In this case it is important to divide the cost over a conservative amount of projects to get a realistic idea of how much the project is “paying” for it.
Most tools and equipment have an ongoing maintenance cost which must be factored into its project cost.
Materials & Supplies
This includes the items that become part of the finished product, like timber for a log home or gravel for the driveway. Often these items are quoted by the unit, such as per foot of timber. Normally you have to order more quantity than will be used in the finished product, because:
- The material is not produced in the exact lengths required.
- The project will generate some waste.
A contingency factor can also be used on the overall quantity to account for unexpected issues during the course of the project.
When there are many small supplies that are too small to track individually it is generally recommended to include a catch-all item, for example “Landscaping Supplies.”
Other Resources
For larger projects, or where greater project management effort is justified, the following resources can also be used.
- Organizational/Administration. The portion of the organization’s administration cost that the project must pay for.
- Subcontractors. These can be tracked as a fixed cost item within a task.
- Facilities. The purchase or rental of buildings to perform the work.
- Financing costs. The interest cost for loans required to carry out the project.
- Contingencies. Where the complexity of the project justifies contingencies as separate resource items, they can be tracked separately.
- Overtime pay. This applies to people as well as to equipment where the rate increase after a certain point in time.
Direct vs. Indirect vs. Overhead
Of course, the CEO’s salary has to be spread out over all projects. In fact, every project has things that are only partially paid for by the project, like tools, bulk fuel purchases, and accounting.
Each project resource falls into one of three categories:
- Direct. Work that results in production units. For example, the hourly unit rate of a laborer, or unit rate for a piece of equipment. The actual cost should be divided into a reasonable number of projects that the resource will be shared across. It must also include the secondary costs like benefits, retirement contributions, bonuses, and any other expense associated with the resource.
- Indirect. Work that is required to produce deliverables but doesn’t directly translate into production. This includes things like quality control, production supervision, and yes, project management. This type of resource needs to be included in estimates to give an accurate project cost. It needs to be divided into each task and allocated as much as practical.
- Overhead. Organizational administration costs like CEO’s salaries are not attributable to the project but, depending on the organizational structure, sometimes must be paid for by all projects. The difference between indirect expenses and overhead is that the indirect expenses are attributable to the project (must be performed to complete the project) whereas overhead doesn’t necessarily have any project involvement. Most project based organizations determine the yearly administrative expense and divide it by the number of projects to arrive at a burden rate on individual projects (or on a resource level, like employee charge out rate) for the following year.
Project Resources in PM Theory
In the Project Management Body of Knowledge (PMBOK) this step is defined within the Estimate Activity Resources process.
During the project planning phase, the project has already been divided into tasks, and each task must be assigned resources.
PMBOK, 5th Edition, Section 6.4, “Estimate Activity Resources”
Estimate Activity Resources is the process of estimating the type and quantities of material, human resources, equipment, or supplies required to perform each activity. The key benefit of this process is that it identifies the type, quantity, and characteristics of resources required to complete the activity which allows more accurate cost and duration estimates.
Estimating Techniques
Generally, you would perform task estimates from the bottom up, meaning each task is given an estimate which is then rolled up into the overall project estimate. Naturally, this is called Bottom Up Estimating. Within each task then, you can employ one (or more) of three estimating techniques:
- Analogous Estimating. This is when you make an analogy to the same, or similar, task that has been performed before. This is the best source of information because actual work completed is extremely reliable, even if it requires adjustments. For example, if your project is for building a driveway and you’ve done it before, you clearly have a head start. Even if you have to make some adjustments, the starting point is tremendously valuable.
- Parametric Estimating. In this method the work is drilled down into a unit cost, for which an estimate exists from published data or prior experience. For example, the cost per square foot of log home can be gleaned from previous projects. In the construction industry almost everything is done this way, from the engineering time down to the construction materials.
- Three point estimating. If you’re not sure how much of a resource is required but can readily put an upper and lower bound on the value, this method is for you. With a three point estimate you choose an optimistic (a) and pessimistic (b) estimate in addition to the normal, most likely (m) one. Then a distribution can be chosen to arrive at the final estimate.
- Normal distribution: te = (a + m + b) / 3.
- Beta distribution: te = (a + 4m + b) / 6.
Resource Calendars
A resource calendar is consulted to determine if the resource is available. This can range from a simple listing of when an employee will be on vacation to a sophisticated software tracking tool.
Example
Here’s an example project resource list. It is broken down into tasks and each task is assigned resources, including a quantity and cost estimate.
110 – Excavation | ||
---|---|---|
Type | Average Use | Total |
Excavation Contractor | Lump Sum | $15,000 |
Bob | 10 hrs @ $50/hr | $500 |
Gravel | 50 m3 @ $100/m3 | $5,000 |
Dump Truck | 15 hrs @ $200/hr | $3,000 |
TOTAL | $23,500 |
Good luck! If you got this far, you have the knowledge you need to estimate your project resources, and to make sure you never end up as the carpenter that forgot the hammer.