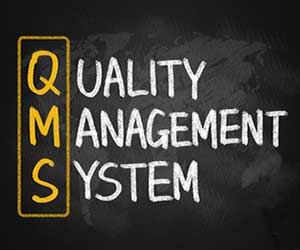
Many people are confused by the difference between these two terms, even experienced professionals. Trust me, the boundaries between them are sometimes grey.
However, there is a difference. And once you realize it, you’ll be amazed at how obvious it is.
Objective
They have different objectives.
- Quality Assurance (QA) focuses on preventing defects.
- Quality Control (QC) focuses on the identifying defects.
The measurement of widgets coming out of an assembly line, a common reference for most people, is Quality Control. In contrast, Quality Assurance measures the assembly line itself, for the purpose of increasing QC results.
Definitions
According to the American Society for Quality (ASQ), the two terms are defined as:
- Quality Assurance is the planned and systematic activities implemented in a quality system so that quality requirements for a product or service will be fulfilled.
- Quality Control is the observation techniques and activities used to fulfill requirements for quality.
Goals
- Quality Assurance seeks to measure the processes and systems in order to reduce defective products. It is often used by management to make decisions on process improvements.
- Quality Control seeks to measure the number or quality of the final products. It is often used to accept or reject products, or for payment.
For example, measuring the number of defective widgets is QC. This information can be used for payment or for acceptance/rejection of units prior to shipment. QA, on the other hand might involve measuring the number of defective widgets produced by each worker, to improve the process of producing the widgets.
Example #1
In a factory that produces pens, a QC manager measures the number of defective pens leaving the production line. The defective items are counted, defects logged and then rejected.
If the most defects are related to the ink, the QA manager might measure the results from the ink injection machine and recommend improvements.
Example #2
In an asphalt paving project, the QC team is employed by the Contractor which takes core samples from the new pavement after it has hardened. The QA team is employed by the owner (State, County, etc.) who obtains cores on a regular basis and compares them with the contractor’s results to ensure the QC process is working.
Example #3
For a software development project, the QC manager tests the code after it is written. The QA manager develops standardized code blocks (functions, etc.) and ensures that the resources are in place to most efficiently and effectively create the highest quality product.
Quality Control (QC) involves the measurement of defects coming out of the final assembly line. It is what most people who are confused about these two terms are thinking of. Quality Assurance (QA) involves the measurement of the process to identify improvements within the process.
Quality Management System
Quality Assurance and Quality Control exist within a Quality Management System (QMS) who’s goal is to maximize the quality of the deliverables of a project or product.
A Quality Management Plan identifies the structure of the Quality Management System. It contains the following parts:
- Quality Standards
A listing of the quality standards that apply to the project/product. Most industries have well developed standards from the owner of the project, or if not then a standard can be purchased from a standards organization such as ANSI, IEEE, or ASTM. - Quality Control
It identifies what will be measured, how often, and what the acceptance/rejection criteria are. This section should also include the applicable inspection forms. - Quality Assurance
It identifies the QA activities, which usually include regular quality audits of the various processes at specified intervals. It might also include reporting criteria for performance of the quality system and potential improvements to the system. Since QA is a process of continual improvement, it is not usually possible to identify every aspect of process improvement up front, however laying the groundwork can give the project team a head start.
Continuous Improvement
Continuous Improvement is a cornerstone ISO-9001, the gold standard for certification of an organization’s Quality Management System. Although there are not many black-and-white rules within ISO-9001 due to the many differences in quality standards from industry to industry, continuous improvement is one of them, and rightly so.
The Quality Assurance system should be structured as to ensure that the process are always looked at critically with room for improvement no matter how much progress has already been made. Continuous Improvement dictates that there is never enough QA. That is, when quality improvement has stopped, quality is effectively moving backwards.