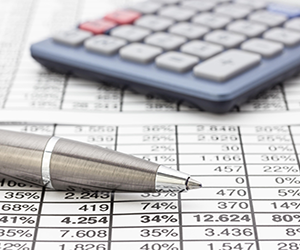
Estimating a project is one of the most important aspects of project management. Projects are by definition temporary endeavors with a defined beginning and end, hence stakeholders need to know how much expenditure they are committing to.
Thus, project estimates tend to start before the project even begins and are usually updated throughout the project life cycle.
The Detailed Estimate is generally considered the third out of five project estimate types. It represents the complete (or almost complete) project or product design. The five estimate types are:
- Conceptual, or Rough Order of Magnitude estimates are produced prior to project initiation, to prioritize the project or decide whether to proceed with it.
- Preliminary estimates are used to decide between several options, within the project.
- Detailed estimates utilize the complete (or almost complete) design of the product or project. Hence, the quantities of resources are known but not the costs.
- Definitive estimates utilize firm cost information, for example, quotes or tenders.
- Final estimates are performed after the project is complete. They are more of a summary of project costs.
How to Produce a Detailed Estimate
Detailed estimates utilize bottom up estimating techniques to estimate individual project tasks and roll them up into an overall project estimate. The process is as follows:
- Calculate Quantities
Each project task is estimated by calculating the quantities of resources, materials, tools, and incidentals necessary to perform the task. - Estimate each task
Analogous or parametric techniques are used to estimate the task. Expert judgment is consulted when available. - Produce Project Estimate
Each task estimate is rolled up into an overall project estimate.
Quantities of materials and resources need to be calculated to the best possible extent. In the construction industry (where I hail from), detailed estimates utilize all of the building design information, that is, quantities of every door and window are itemized and placed into a spreadsheet.
To the extent that quantities of resources are not calculated to precision, the estimate is that much less accurate.
Analogous Estimating
Analogous estimating refers to the estimation by comparing to similar projects. You cherry pick a project that’s deemed similar enough to give you the best cost information.
For a detailed estimate, analogous estimating happens on the task, as opposed to the project, level. Each task is compared to actual costs for that task in the previous project. For example, the new building has 15 doors, and a certain previous building that was built had 10 of the same doors, therefore we will add 50% to the actual cost for that item to produce the new estimate.
You can cherry pick different projects for different items. For example, if the doors are similar to the doors on Previous Building A, but the windows are the same as the windows on Previous Building B, therefore we will use Buidling A for the doors and Building B for the windows.
Parametric Estimating
Parametric estimating utilizes unit rates which are usually averages of many different projects. They account for alot of different variables that have occurred on many projects, and can often be obtained from industry associations that track average costs (each organization’s cost data are usually top secret). They can also be obtained from internally tracked cost information.
For example, we might know that installing doors costs $450/door, therefore we simply multiple by the number of doors to be installed.
Adjustments
Adjustments to the analogous or parametric information are important to get the estimate just right and utilize all the information you have.
For analogous estimating, adjustments to the estimate are based on known differences between the current project and the cherry-picked previous project. For example, if the doors were 10% larger than the previous project, you could add 10% to the estimate.
For parametric estimating, you are analyzing the deviation of your project from the average of many projects, so you need to consider how the current project is different from the average. For example, if these doors are 25% smaller than the average door, you may want to reduce the estimate by 25%.
Accuracy
Detailed estimates are generally accepted to be in the range of -5% to +10%. That is, a $100,000 estimate has an acceptable final cost range of $95,000 to $110,000.
How do you obtain this accuracy, or know what it is? This is a good question, without an easy answer. This is because there is an art and a science to it.
The science is relatively simple. When you know that each task has a variance of -5% to +10% when performed many times, you know that the overall estimate has the same variance. However, each task needs to be analyzed accordingly. In many cases it is possible to look at the same task which has been performed many times. If not, you can usually break it down even further and analyze subtasks until you get to a unit that’s small enough to put an accuracy range on.
The overall project estimate accuracy is the weighted average of each task. For example, if a project contains only two tasks, Task A and Task B, and they are the exact same size:
- If Task A has an estimate with an accuracy of 10%, and
- If Task B has an estimate with an accuracy of 20%,
- The accuracy of the project estimate is (10 + 20) / 2 = 15%
This is valid as long as the number of hours/resources in each task is the same. But that’s not usually the case. If the tasks are not the same size, the accuracy of the project is the average of the tasks, weighted to the task size.
AccuracyProject = [(Estimate_A x Accuracy_A) + (Estimate_B x Accuracy_B)] / [(Estimate_A + Estimate_B) x 2]
Any tasks that are not within the acceptable range must be refined until they are in the acceptable range. There isn’t really any alternative, because the overall estimate cannot be more accurate than its constituent parts.
However, in practice the process is as follows: The detailed estimate takes into account all of the available design information for the project. If there is still too much uncertainty to assign an accuracy of -5% to +10%, the loss of accuracy is communicated to the project stakeholders as necessary.
Examples
- An engineering firm is tasked with the design of a building. They itemize each component and use cost information from previous projects for each component to produce a detailed estimate, which the owner can use to update their budget prior to obtaining tenders for the project.
- A software development firm receives a project to develop a web application. The number of pages and programming requirements are planned out and itemized in a detailed estimate, which is presented to the client’s board for a decision to proceed.
- A manufacturing plant has grown and begins to hit its plant capacity regularly. The expansion of the assembly lines are planned out and each piece of necessary equipment is itemized. Published cost data is used to determine the detailed estimate, which is used to make a decision to proceed to the next level: Obtaining quotes for the work. Once the quotes are obtained, the estimate becomes a definitive estimate.