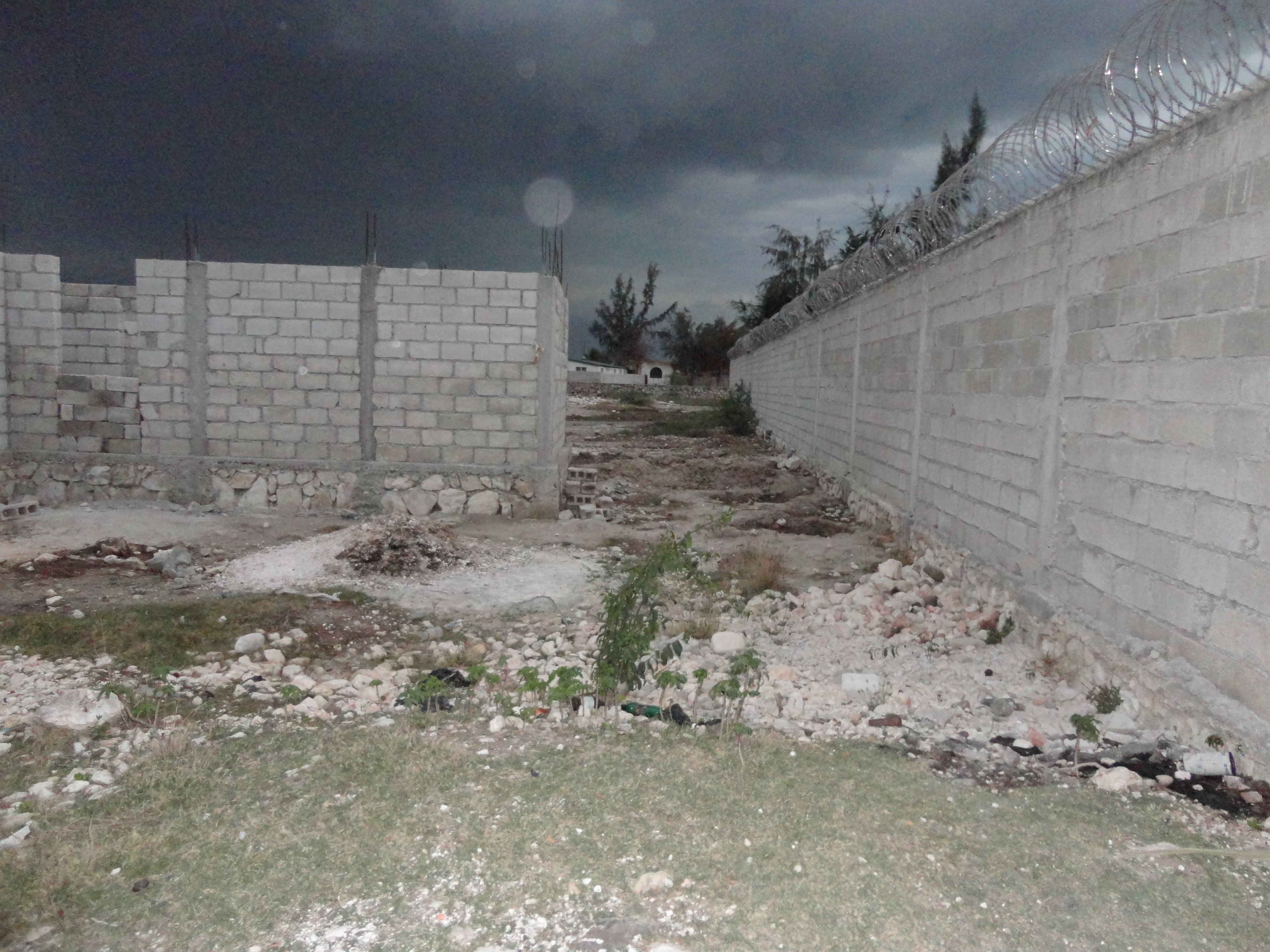
In the engineering business, project quality is important. I’ve seen many projects that did everything right, but derailed based on one single issue the project team overlooked. Don’t let that happen to you.
The Project Management Institute (PMI) identifies project quality planning as the first of three steps to effective project quality management. In this post, I will expand on this step and talk about what we at Roseke Engineering do to plan project quality.
Cost-Benefit Analysis
Make no mistake about it, quality impacts the bottom line. I’ve been an engineering consultant too long to see people slack off on some part of a project thinking that it won’t really catch up to them. And usually it doesn’t immediately. But if furthering your career is important to you, like it is to most people, quality is not something that can be sacrificed. You must make sure all deliverables that you are responsible for are of high quality.
Cost of Quality
PMI says that cost of quality includes all costs incurred over the life of the project or product by investment in preventing non-conformance to requirements, appraising the product or service for conformance to requirements, and failing to meet requirements (rework).
Cost of Conformance
- Training
- Document processes
- Equipment
- Time to do it right
- Testing
- Destructive testing loss
- Inspections
Cost of Non-conformance
- Rework
- Scrap
- Liabilities
- Warranty work
- Lost business
Control Charts
Control charts define the limits of when action should be taken to correct a project variance. For example, you could monitor project hours with a control chart that has time on the x-axis and hours spent on the y-axis. At the project outset five lines are drawn. The first is the planned hours worked, the second and third are the upper and lower control limits, and the fourth and fifth are the specification limits. The control limits are the point at which action must be taken to correct the variance, and the specification limits are the point at which the project is outside the specifications of the project.
Benchmarking
Benchmarking involves the comparison of actual or planned project practice with those of comparable projects to identify best practices, generate ideas for improvement, and provide a basis for measuring performance.
Design of Experiments
This is a statistical method which identifies factors which may influence specific variables of a product or process under development or in production. For example, automotive designers could use this technique to determine which combination of tires and suspension will product the most desirable ride characteristics.
Statistical Sampling
Statistical sampling involves choosing a part of a project deliverable set for inspection, for example, choosing 10 engineering drawings out of 75 for an inspection for certain quality criteria.
Flowcharting
A flowchart of the project schedule can be a great way to show the relationships between various project steps and can be an invaluable tool to find project quality issues. They can help the project team anticipate quality problems.
Proprietary Quality Management Methodologies
Many proprietary methods for managing project quality exist, including Six Sigma, Quality Function Deployment, CMMI, Total Quality Management, Balanced Scorecard, etc.
Brainstorming
Sometimes, getting the project together and brainstorming for potential quality problems is the best way to ensure a high quality outcome.
Affinity Diagrams
These are a great tool to visually identify logical groupings based on natural relationships. They can draw out the potential quality issues in a snap.
Force Field Analysis
Diagrams of the forces for and against change. Before any project changes occur, this is an interesting way to make sure that quality remains high throughout.