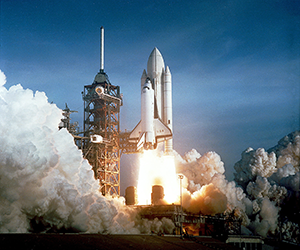
In 1986, the NASA Space Shuttle Challenger exploded spectacularly upon take-off in front of one of the largest live TV audiences in history (to that time). The investigation concluded that several tiny O-rings that sealed the rocket booster to the fuel supply failed. These O-rings were about 1 foot in diameter.
Just like the tiny O-rings were able to bring down the mighty Challenger, one small underestimation can result in a chain reaction that the project can’t recover from. Therefore, project planning needs to make sure that enough resources, costs, and time are assigned to each task. The Challenger’s engineers no doubt wished they could have spent more time perfecting the O-rings.
These estimates are then used to construct the project schedule.
Estimating Techniques
The four types of estimating methods are:
- Analogous Estimating
- Parametric Estimating
- Three point Estimating
- Expert Judgment
Analogous Estimating
As the name suggests, this is when you make an analogy to the same, or similar, task that has been performed before. This is the best source of information you have because actual work completed is extremely reliable even if it needs adjustments. In fact, many project-based organizations have numerous similar projects, and this is the natural starting point. Here is a checklist of potential adjustments:
- The task is bigger or smaller than the last one.
In this case, scale the duration up or down by the appropriate amount. For example, the log house has slightly more square footage, or the driveway is longer, or several more windows have been added. It’s never the big, obvious things that cause problems for project managers, it’s the little things, and you have to make sure you include enough contingencies for them. - The task needs specialty products or services that the previous one didn’t.
This has equally high potential for project overruns. In this case, add in the necessary products and services and proceed as usual. For example, the slightly bigger roof trusses might require the next larger size of crane. Or the foundation requires removal of rock instead of clay. - The task is for a slightly different end product.
In this case, determine the difference in materials and/or workmanship and figure out the difference in resources, cost, and time. For example, you could calculate from the plans that the log home requires 20% more timber than the previous one. Then you could estimate that the Wood Framing task will take 20% more time.
Analogous estimating is only as reliable as actual data the estimate is being taken from. Unusual incidences are rarely written down and remembered for future projects, but can seriously derail the estimation of the next project. For example, if the crane broke down and spent four days on site instead of two, you would not need to necessarily account for that in the new estimate.
Also, the productivity of the work is an important consideration. For knowledge workers such as engineers, adding more of them sometimes slows the production and decision making process down instead of speeding it up. Also, a very experienced laborer has higher productivity than a less experienced one. Thus, if the previous project used an inexperienced laborer to place the roof trusses, and this time you will be using a more experienced one, the estimate can and should be different.
Parametric Estimating
This method involves drilling down into a unit cost. Here are some examples:
- Total construction time per square foot of log home.
- Pouring time per cubic yard of concrete.
- Installation time of carpet per square foot.
In the construction industry, where I come from, almost everything is done this way. For example if the log home company kept track of the construction time, especially for the individual task of Wood Framing together with the square footage of the home, they could eventually arrive at a pretty good parametric estimate for all of the task durations. In fact, a parametric estimate of the entire project would serve as an excellent double check (Cost or Duration per square foot of home).
If your company is project-based and has many similar projects, you need to make sure these parametric estimates are available and updated regularly.
Sometimes a parametric value includes fixed items, such as doors and windows which require a fixed time for installation regardless of how much timber is required to construct the whole house. In this case the fixed items can be separated out and added to the overall parametric estimate.
Three-point Estimating
In this method, the estimator determines three values:
- Optimistic
- Most Likely
- Pessimistic
The second, “Most Likely” is the average of what the task duration would be if performed many times, in other words the normal estimate using other methods. The other two represent the upper and lower bounds that you are not likely to exceed.
To do this numerically, you would first assign a confident interval for the upper and lower bounds (optimistic and pessimistic values), such as 90%. Many textbooks use 99% or some other value – the methodology varies. But if you have 10 previous projects to consult from and can determine what value 1 out of the 10 projects exceeded, you can run with that.
Generally one of two distributions is used. The triangular distribution is simply an average of the three estimates and the beta distribution is a bit tighter.
Triangular (average) distribution | Beta distribution |
---|---|
te = (a + m + b) / 3 | te = (a + 4m + b) / 6 |
Where:
- te = Expected duration
- a = Optimistic
- m = Most likely
- b = Pessimistic
The triangular distribution will skew the results to the value which is farther away from the Most Likely value. The beta distribution also does that but tightens up the distribution (closer to the Most Likely value).
I don’t believe there’s any more rocket science involved than that, unless you want to determine the failure probability of the rocket booster O-rings. You simply have to decide how tight to the Most Likely value you want to be, and choose the distribution accordingly.
The standard deviation of the distribution is:
σte = (b – a) / 6
If you add up all of the durations (∑m) and standard deviations (∑σ) for each task, you will have the total project duration as well as it’s standard deviation. You can draw the following conclusions from this:
- The confidence level in one standard deviation, i.e. M ± σ is 68%.
- The confidence level in two standard deviations, i.e. M ± σ is 95%.
- The confidence level in two standard deviations, i.e. M ± σ is 99.7%.
Just don’t be fooled by fancy statistics that make the conclusion sound more reliable than the input data. In other words, garbage in, garbage out.
Expert Judgment
Professional estimators will tell you that in spite of all the techniques in the book, a technical expert will be the best resource you could ever have. In fact, they could be the only resource you need for estimating. Technical experts are notoriously busy because their expertise gets used on many projects. But if you have access to one, whether inside the company or out, you should find a way to use them.
But what if a technical expert contradicts the other methods? For example, let’s say you’re installing carpet and your carpet installer tells you a certain project will take 4 days, but past experience (analagous) is telling you it will take 10 days. How valuable is the expert’s opinion then? In this situation, consider the underlying data of each method. For example, maybe this carpet installer frequently underestimates duration, or the past experience estimates are skewed by a certain piece of data.
Project management itself does not exist independent of the technical expertise inherent in the project. That is, the project manager or management team must be at least passingly familiar with the technical aspects of the work or the project has little chance of success.
Resource Calendar
A Resource Calendar tells a project manager when a resource is available. For example,
The excavator is at Jobsite X from January 1 to February 12
It can range from a simple statement such as the above, to sophisticated tracking tools via project management software.
Example Project
To make an estimate to build our log home, we would inspect the resource table developed for each task and determine the resources, cost, and time required. The resources are effectively an intermediate step, because their availability is necessary to determine the cost and duration.
I’m going to demonstrate using the task Wood Framing and all the other tasks are similar.
The expected duration of the task Wood Framing is 18 days (m = 18), but there is significant potential for delays. The Optimistic estimate is 15 days (a = 15), but the Pessimistic estimate is 33 days (b = 33). The beta distribution yields:
te = (15 + 4 x 18 + 33) / 6 = 20 days
Therefore, the original estimate was 18 days but because of the potential of reaching as high as 33 days, the estimate is increased to 20 days.
The standard deviation is (33 – 15) / 6 = 3.0. Therefore, the task duration is:
- 20 days is the official estimate.
- 23 days with 68% confidence.
- 26 days with 95% confidence.
- 29 days with 99.7% confidence.
We will use 20 days instead of 18 in the estimate but the confidence intervals can be used to determine completion dates with certain confidence intervals, or add contingencies during the schedule development phase.
Task ID | Name | Durations | Cost |
---|---|---|---|
110 | Excavation | 6 days | $5,850 |
120 | Pour Foundation | 10 days | $4,700 |
210 | Wood Framing | 20 days | $60,850 |
310 | Electrical & Plumbing | 10 days | $20,260 |
320 | Flooring | 8 days | $18,760 |
330 | Finishing | 12 days | $16,760 |
410 | Landscaping | 14 days | $7,620 |
TOTAL | 80 days | $134,800 |
Next Steps
After the project is estimated, the schedule development phase puts the tasks on a graphical schedule. The total (80 days in the example) will be decreased because some tasks will occur in parallel and resource usage will be smoothed so that resources are used at a constant rate as much as possible (this is called resource levelling).
As you can see, you don’t need to be a rocket scientist to be a great estimator, but even rocket scientists can use project estimation techniques to make sure their projects go smoother.