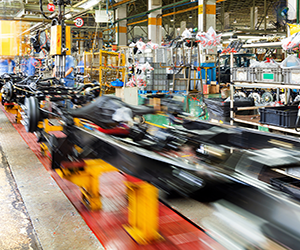
The Theory of Constraints relates any complex system, such as a manufacturing plant, to a set of one or two constraints which fix the upper limit on its performance. It seeks to manage those constraints to maximize the performance of the plant.
The Theory of Constraints was developed by Dr. Eli Goldratt and first published in his book The Goal in 1984. It was followed up with an adaptation to project management in Critical Chain (1997).
The Three Constraints
All businesses have a common goal: To make a profit. This goal is constrained by three variables:
- Throughput
The rate at which the business generates revenue through the sale of goods. - Operational Expense
The expense incurred to turn the inventory into throughput. - Inventory
The cost of the products that are to be sold, from raw material through to finished goods.
To turn an investment into profit, an entrepreneur must build a plant (operational expense), buy the raw materials (inventory), and find a willing buyer for the products (throughput).
Only one of the three constraints will be the limiting factor at any time, for example if the demand for the product is higher than the ability to produce it, throughput is the limiting factor. If there is not enough inventory to produce the products, inventory is the limiting factor and funds must be found to purchase the raw materials.
Bottlenecks
Maximizing throughput is accomplished by identifying the “bottlenecks,” that define the other two constraints, operational expense and inventory.
There are five steps to maximizing throughput:
- Identify the system’s bottlenecks
Most plants have one machine or process whose productivity defines the productivity of the whole plant, and every other process has a little bit of downtime. This bottleneck must be identified. - Decide how to exploit the bottlenecks
Once it is clear what the constraint is, any easy productivity gains to exploit the bottleneck, such as performing maintenance in the evening, or adding a staff member for machine changeovers, should be performed. - Subordinate everything else to the above decision
Make sure that the whole plant marches to the tune of the bottlenecks. The plant’s process flow should be revised to ensure the bottleneck is kept at peak productivity at all times. Buffer stocks should be kept at the bottleneck to ensure it doesn’t run out of material. Other processes which supply the bottleneck should ensure that its raw materials are produced at the rate of the bottleneck’s production. - Alleviate the system’s bottlenecks
Anything that can be done to take pressure off the bottlenecks, like putting an old machine back to use in parallel, or optimizing the machine’s performance, need to be implemented. - If, in a previous step, a bottleneck has been broken go back to step 1
The previous four steps can increase the bottleneck’s production ahead of another process so that it is no longer a bottleneck. In this case the five steps must start anew until the plant is performing at maximum capacity.
This is purely an optimization exercise, and capital expenditures designed to expand production is not part of the theory (although perhaps small ones might be part of the optimization process). For example, buying another machine to double the production in your bottleneck is a financial decision that must be made in light of market demand for the product, and is outside the scope of the Theory of Constraints.
The Theory of Constraints does increase production, but it does this by optimizing process flow within the plant. In TOC-speak, we would say that purchasing new machines (or hiring new people) to alleviate the operational expense constraint will make the primary constraint flip from operational expense to throughput (finding a willing buyer). Hence, you cannot spend your way to prosperity – you are always constrained by one of the three constraints.
Performance Metrics
The Theory of Constraints can wreak havoc on traditional performance metrics, which tend to measure the uptime of machines and people. After implementing the theory, this uptime will decrease for many people and machines that are not working on the bottleneck, creating poor operational metrics. But if the bottlenecks are producing faster, the whole plant is producing faster, and therefore its profitability is higher. The plant is more profitable in spite of potentially lower utilization in certain places.
In addition, it is easier to judge how much production the plant is capable of. Since the production rate of the bottlenecks is equal to the production rate of the plant, customers can be given better estimates of when their orders will arrive, thereby reducing late orders, increasing customer satisfaction and hence generating more future orders for the product.
Buffers
Buffers are placed before and after a constraint (bottleneck) to ensure it is never starved for raw materials and to protect it from variations and unexpected events within the plant.
Buffers can be stacks of inventory (raw materials), time, factory floor space, or anything that ensures the bottleneck will not stop operating at peak productivity levels. In the critical chain method (the project management adaptation of the Theory of Constraints) time buffers are the central concept.
Defects and Rework
When a product must be returned to a bottleneck process to be reworked, the entire production process has been wasted. The entire plant’s output has stalled for an entire production cycle, and the plant has produced two products while creating throughput for only one. This is effectively the most egregious loss of throughput possible, and several remedies exist to ensure zero defects by the bottleneck processes:
- Additional inspection and monitoring of product quality at the downstream end of the bottleneck can cost more, but catch more wasted production. Rather than reduce inspection to save money, increase it at the bottleneck and work to improve the machine to eliminate all of the rework.
- Quality control activities can be placed before the bottleneck instead of behind it, if possible. The individual raw materials can sometimes pass inspection prior to being processed by the bottleneck, to prevent material from going back through the bottleneck twice.
Remember, any improvement in the bottleneck process is an improvement for the entire plant.
Learn More
To learn more about the Theory of Constraints, the following resources are available:
- The Goal: A Process of Ongoing Improvement, (original 1982) by Dr. Eli Goldratt, represented the original introduction of the Theory of Constraints to the world. It has been updated five times. It is in a unique novel-style format.
- Theory of Constraints (1990) by Dr. Eli Goldratt provides more detail about how to implement the Theory of Constraints
- Critical Chain (1997) by Dr. Eli Goldratt, introduces the project management adaptation of the Theory of Constraints
- Theory of Constraints International Certification Organization (TOCICO) maintains the up-to-date body of knowledge and provides certification for the Theory of Constraints.