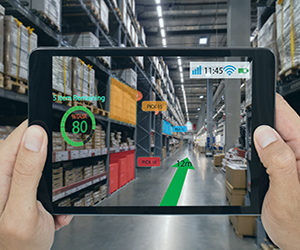
Many people have heard of Just-in-time manufacturing. But how does it really work, and how can you use it to improve your operations?
Most importantly, what are the risks when there is a hiccup in the supply of parts?
Just-in-time manufacturing originated in post-war Japan, where there were neither raw materials nor space to build large factories, hence manufacturers had little choice but to operate in small quarters and maximize the efficiency of the production process. The success of Toyota Motor Company, and japanese manufacturers in general, lead to heavy interest in the Toyota Production System. When Toyota started opening up about the secret of their success in 1988, just-in-time manufacturing was the most easily recognizable component and instantly became a buzzword.
Today, the term just-in-time manufacturing is sometimes used interchangeably with the Toyota Production System, although it was originally just one part.
Meanwhile, the Toyota Production System and just-in-time production have evolved into a component of the more general concepts of Lean Manufacturing.
What is Just-In-Time Manufacturing?
Just-in-time manufacturing is a management strategy that seeks to improve efficiency by minimizing on-hand inventory. In the case of a car manufacturer, the component parts are available on the assembly line in the lowest possible quantity.
Just-in-time is essentially a way of thinking. In many plants, managers attempt to have the most, rather than the least, component parts available in order to reduce the risk of stopping the assembly line. And there is some validity to this line of thinking.
But the success of the Toyota Production System and the subsequent rise of Lean Manufacturing are converting many people to the opposite.
How Does Just-in-Time Work?
In the Toyota Production System, every assembly task is specified in minute detail in a written procedure, which eliminates variation. Every bolt and weld is itemized, sizes and torques specified, and assembly times specified.
In non-Lean plants a station worker might be assigned to place and tighten four bolts, whereas in a Toyota plant there would be a written procedure that specifies how many bolts, in what order, how far they would be turned, and how many seconds it should take. Thus, there is no room for variation, which increases quality.
More importantly, a designated person is specified to refill of the parts inventory in the assembly line. Not a parts department or inventory division, but one person who’s responsibility is to ensure the parts are available at each station. There is still an inventory division from which that person gets the parts, but the designated supplier is responsible for getting them and re-stocking the assembly line.
Because the procedures are so well documented, workers don’t spend their time thinking about what they are doing. Rather, they are empowered to make small improvements in the procedures. This is accomplished via a system of kanban boards which measure the cycle time across the assembly line and tracks the implementation of process improvements.
How Much Money Does Just-In-Time Save?
The cost of on-hand inventory can be significant. When an assembly line is built, the original inventory levels are part of the cost of the assembly line. If they can be reduced by, say, 25%, or 50%, in most plants that results in significant monetary gains.
For example, if the purchase of parts constitutes 25% of the final sale price of a product, and the inventory levels are equal to 40 days of production, the cost of on-hand inventory is the same as 10 days worth of production. That is, the first 10 days of production pay for the parts. If you can cut inventory levels in half, you could realize 5 days of production to the bottom line, or 5 / 365 = 1.4% profit to the company’s balance sheet.
There are additional savings in the cost of floor space to store the inventory.
How do you Ensure the Assembly Line Doesn’t Stop?
It may seem like minimizing inventory increases the risk of stopping the assembly line, and there is some merit to this. It is true that Just-in-time manufacturing needs to be executed well to be successful.
There are two keys to minimizing the risk of running out of inventory:
- Maximize the number suppliers. If you have only one supplier, something can happen to that supply chain that could shut down your assembly line. However, if you have several to choose from, the others can jump in and produce more.
- Lean manufacturing methodologies use a system whereby the product is in continuous movement throughout the entire production process, from raw material to finished good. Lean production moves the inventory in continuous flow. When executed correctly, lean manufacturing does not need significant quantities of inventory on the floor.
Indeed, Toyota experienced a fire at a supplier’s plant in 1997 which caused the assembly line to stop. This led them to institute a policy of multiple suppliers which remains in place today.
Just-In-Time vs. Lean Manufacturing
Today, just-in-time manufacturing is a component of the larger methodology of lean manufacturing. Lean manufacturing involves five components:
- Identifying value
Value is determined by the customer. The price they pay for the products being produced is the baseline for determination of the value stream. - Determining the value stream
The production of the product results in a value stream, which is the set of activities that is necessary to produce and deliver the products to the customer. These activities are mapped in a process called value stream mapping, which analyzes and improves the flow of information and materials necessary to produce the products. - Flow
Once it enters the production process, raw material proceeds all of the way through to finished good without stopping as inventory along the way. This is one of the fundamental tenets of lean, that instead of attempting to maximize the uptime of people and machines, the goal is to move the inventory through the system (and hence into the hands of the customer) in the smallest amount of time. This requires a series of equally time-spaced production steps. Increasing production is done via multiple, parallel production lines, leading to smaller machines and quicker changeover times for different product variants. Organizations that convert to lean often report reductions of greater than 90% in the time an item starts production to when it enters the hands of a customer, which substantially enhances business cash flow. - Pull
The products are produced in response to customer demand. Because the first finished product comes off the assembly line in days or hours instead of months, the plant can wait until an order is placed to start moving the production line instead of making large machine changeovers followed by large batches of production that may or may not sell (or sell for a discount to get rid of them). The presence of multiple, parallel assembly lines leads to small machines that are quickly changed over to product variations. The pull system is governed by kanban, which involves producing a card (either physical or within an electronic tracking system) which moves with the product from start to finish, specifying all of the production steps necessary to produce it. - Continuous Improvement
Workers are empowered to make continual, small improvements, called kaizen, to the assembly process. Over time, the processes and procedures are perfected. Any item that is not completely necessary for the production of the products is considered waste and must be removed from the process. The cost of inventory (storage, purchase, etc.) is the second of seven types of waste identified by Toyota, and part of the 8 types of waste (one more was added) in modern Lean Manufacturing.
Just-in-time manufacturing was a major building block in the transformation of modern industrial society, and there is no doubt that its concepts can make any business more efficient. When management thinking reverses from maximizing inventory to minimizing it, the benefits can be enormous.