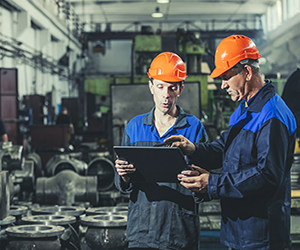
Human beings are naturally predisposed to resist change because of the risks it entails. Maybe the change will fail. Maybe it will reduce business or personal income. And maybe it will result in a loss of job security.
We’d rather the devil we know, than the devil we don’t.
But process improvement is often an exciting step forward that makes an important contribution to the business. Hence, it needs to be approached with passion and a sense of adventure. Deep within, everyone does want to try something new, move forward, and feel a sense of accomplishment. There is no question it is necessary in the full spectrum of job satisfaction.
The key to improving your processes is to implement the right methodology. Every business has a written methodology that was developed for their industry or sector. One or more of the following six methodologies will apply to you.
- Lean
- Six Sigma
- Project Management
- Agile
- Theory of Constraints
- Lean Six Sigma
Lean
Lean production developed out of the Toyota Production System after Toyota emerged from ruins after World War II to become the world’s largest auto manufacturer in the 1980’s. As such, it is ideal for manufacturing plants where a large number or continuous stream of products (widgets) are produced.
Lean manufacturing is a process improvement method that involves five main components:
- Value
Value is something that someone is willing to pay for. Hence, the first step is to identify the item of value. In the case of Toyota, this is the car. - Value stream
The value stream refers to the process required to produce the item of value. It is often communicated in the form of a graphical value stream map which clearly identifies each of the individual processes which result in value, such as cutting, stamping, and painting. - Flow
In lean manufacturing, the goal is to ensure that a product does not spend any time waiting as idle inventory anywhere throughout the production process. That is, as soon as the raw material enters the first production station it does not stop until it becomes a final product. This means that there are no large stacks of inventory on the production floor. Raw materials entering the assembly line at intermediate stations are delivered as needed in a process called just-in-time manufacturing. If higher production is necessary, multiple parallel assembly lines are implemented. This results in smaller machines which reduce changeover times for different product variations. In addition, the assembly line is synchronized so that production time is the same for all stations in the process, called the takt time. - Pull
Lean manufacturing specifies that the customer initiates the production process. When a customer orders a product, the production machines are switched over to the product specifications in a system called kanban and the production starts. Because the product proceeds all of the way through the assembly process without stopping, the customer can receive the first shipment quickly, and determine if any changes should be made. - Continuous improvement
The assembly line is continuously and rigorously inspected for waste (called muda) which does not add value to the production process. Waste is relentlessly eliminated, not with meetings or budgeting sessions, but through immediate action on the production floor. Toyota even implemented a system whereby any production line worker could (actually, was responsible to) stop the production line to correct a quality problem immediately. Far from leaving the inmates in charge of the asylum, it produced very high quality levels that Toyota’s products are still known for.
In contrast to traditional manufacturing which seeks to maximize the uptime of large, expensive machines and people, lean manufacturing has multiple, small machines which can be changed over and maintained quickly. In addition, the machine operators and plant personnel may not be fully utilized, but the production speed, quality, and footprint are maximized, maximizing profits, which is the larger business goal.
Six Sigma
Six Sigma was developed by Motorola but popularized by General Electric CEO Jack Welch in the 1990’s. Hence, like Lean Manufacturing, it is a process improvement method oriented towards manufacturing operations.
Six Sigma focuses primarily on product quality. When a large number of widgets are produced, the quality (based on a quantifiable metric such as length, color, strength, etc.) looks like a bell curve, for example,
The “standard deviations” are statistical divisions whose percentages are fixed. A standard deviation is noted by a greek letter sigma (σ).
The goal of Six Sigma is to limit the defects to 3 standard deviations from the mean in either direction. When the defects are measured outside of this band, a process called DMAIC (pronounced “de-may-ic”) is initiated to implement the corrections:
- Define the problem, as well as the metrics which are most important to measure success. This includes defining the Critical-to-Quality (CTQ) issues.
- Measure the current processes to determine and document the baseline performance.
- Analyze the causes of the defects. Many techniques can be used in this phase including Pareto Charts, Fishbone Diagrams, and Regression Analysis.
- Improve the process by implementing the process improvement and testing various alternatives.
- Control. Implement controls to ensure that the defect does not re-occur over time.
Project Management
In organizations that deal with unique projects with a defined beginning and end, and whose product can be one unique item (or just a few), project management methodologies could be the answer.
There are three main project management methodologies in use today:
- The Project Management Body of Knowledge (PMBOK Guide) is the most popular and also the most comprehensive. It divides projects into 10 knowledge areas and 5 process groups. The knowledge areas are used anytime throughout the project (for example, scope management or schedule management), whereas the process groups are roughly chronological (for example, planning, execution, etc.).
- PRINCE2, which stands for Projects in Controlled Environments, was developed by the UK government but is today administered by Axelos, partially owned by the UK government. Hence, it is most popular in the UK, although it is gaining popularity throughout the world. Unlike the PMBOK Guide, PRINCE2 is not a comprehensive project management knowledge bank. Rather, it focuses on the project structure, that is, various project roles are identified, such as project manager, team leader, and project support, and these roles have well defined responsibilities that must be fulfilled. Although some roles can be fulfilled by the same person (especially for small projects) each role is well defined.
- The Individual Competence Baseline (ICB), published by the International Project Management Association (IPMA), certifies project managers based on a list of 29 “competence elements” for example, leadership, teamwork, and negotiation. The ICB is administered in each country through “member organizations” of the IPMA, who are free to make modifications to the ICB to account for local business conditions, however most adhere relatively closely. The ICB is intended as a certification program for project managers rather than a project management methodology, but its competence elements effectively create a methodology to be followed by a project manager.
Agile
In the project management space, agile methodologies are gaining traction. Agile originated in the software development industry but has gained limited traction in the wider project management space.
Agile methods are suited to projects that have a poorly defined or fluid scope, such as software or research and development projects.
Agile project management focuses on iterations, called sprints, rather than planning and execution of the entire project in detail. Each sprint lasts 1 – 4 weeks and is planned and executed with a focus on creating value with shippable product releases. For example, a software product demonstrates a new, functional and tested software to the customer after each sprint. The final product, as envisioned, can be released to the market in partial increments (as determined by the product owner).
Theory of Constraints
The Theory of Constraints was developed by Dr. Eli Goldratt in the 1980’s. It was intended for manufacturing operations and followed up by Critical Chain Method for project management. Although it has a smaller following than lean manufacturing or six sigma, it is very loyal and the Theory of Constraints International Certification Organization (TOCICO) maintains a certification scheme for this process improvement methodology.
The Theory of Constraints looks at a manufacturing operation from the point of view of “bottlenecks,” or constraints. A plant’s production speed is usually equal to the speed of one or two machines which limit its throughput. These bottlenecks need to be fully utilized, that is, other processes need to be prioritized to ensure that raw material is available to the bottleneck without interruption. Control and testing procedures need to be arranged to maximize the bottleneck’s uptime. Sufficient “buffers” need to be in place to account for unexpected events.
Non-bottleneck processes, on the other hand, have a different prioritization method. They need to ensure the bottleneck process is continually fed, and that the other processes are supplied to ensure that the bottleneck does not change.
Lean Six Sigma
Although lean manufacturing operations report significantly higher quality metrics than traditional manufacturing ones, the primary defining feature of lean is production speed. Six Sigma, on the other hand, is focused on quality. Hence, the combination of the two has resulted in the concept of Lean Six Sigma.
The two systems have alot in common. They both originated in manufacturing and maintain their roots there. They also spend most of their time measuring variation, that is, the amount that each production station’s output varies from product to product. Variation is an enemy of good manufacturing practice. But lean manufacturing seeks to optimize the production line’s efficiency, whereas Six Sigma measures the end product quality and works backwards.
Although both methodologies have been developed separately and contain extensive bodies of knowledge (and learning curves), the argument for learning both methods, and implementing them both simultaneously, is compelling.
Hence, Lean Six Sigma has developed many practitioners, plus online and offline training possibilities, but it remains a hybrid methodology – there is no central authority.
The Right Way
Improving your business processes can be a daunting task fraught with many issues. What metrics will determine an improvement? Will upper management agree with this metric? How will the metric be improved? What if it doesn’t improve?
Implementing process improvement is a 4 step process:
- Identify the most appropriate methodology for the process
- Lean
- Six Sigma
- Project Management
- Agile
- Theory of Constraints
- Lean Six Sigma
- Determine the baseline
After a complex change to a process, you must be able to look back and quantify the initial state to be able to measure the improvement. Sometimes this is a complex undertaking that involves starting new measurements. In lean manufacturing, a value stream map is used to communicate the current process. - Determine the final state
The end goal is defined, and communicated to management. The design of the new process is initiated and a picture of the final process is in place, sufficient to proceed with the process improvement. - Plan the transition
The transition process often requires production to be maintained, or quality metrics to be sustained at a minimum level. This requires planning of the transition phase. - Implement it
The process improvement implementation phase is one of the most exciting parts of business. Ensure you savor the experience for future reference.